Covered Piping Systems – Best Practices
Covered Piping Systems – Implementing an Inspection Management Program:
ASME B31.1 Power Piping; sets requirements for covered piping systems (CPS). The code specifies that any piping system with a nominal size greater than 4 inches, operating at 750F or above, or greater than 1025PSI shall be categorized as CPS
The operation of pressurized piping systems presents significant safety risks with numerous well-documented global events having been recorded. Consequently, International Standards have been developed prescribing guidelines to promote premature failure detection and overall safety.
Standards detail requirements, recommendations, and guidance for the implementation as the responsibility of the operating company, to exercise control measures to ensure safe facility operations for all Covered Piping Systems (CPS), which include:
- API 570 Section 5 – Piping Code (In-service inspection (4)
- API 574 Section 12 – Records
- ASME B31.1 Covered Piping Systems (CPS) Chapter (VII) Operations & Maintenance
- Non-Mandatory Section (V) V-2 General
- The Pressure Safety Systems Regulations (2000)
Establishing Safe System Management Practices
The standards provide valuable guidance as to the recommended requirements to develop CPS procedures/programs to manage piping systems, and the understanding and application of these recommendations are essential in establishing safe system management practices.
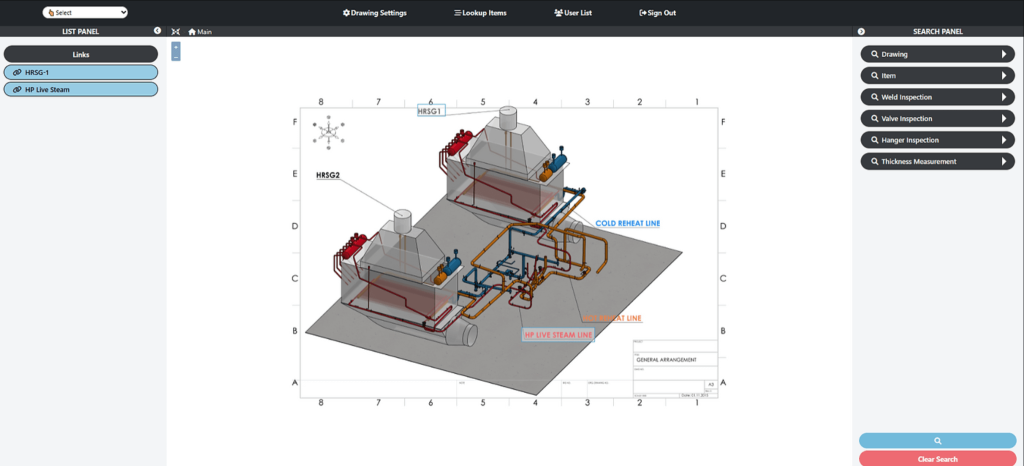
Therefore, operators are responsible for developing, documenting, implementing, executing, and assessing site-specific CPS procedures and programs, and defining the system(s) and the system components to include. Standards define examples and provide guidance listings from O&M procedures to condition assessment. However, the scope of related inspections and inspection applications are completely plant-dependent and may vary.
When constructing a plant-specific system and plan based on present and/or possible types of failure mechanisms, determining key items for inclusion, and formulating an inspection program is key. The scope and inspection intervals are plant-dependent and the responsibility of a competent person, engineering judgment, and current industry best practice shall be considered.
Standards for Covered Piping Systems (CPS)
The standards cover a wide scope for CPS programs, with a focus on inspection; the key considerations being piping weldments, piping support system (hangers), piping controls (valves), piping bends, piping material condition, and applicable material degradation mechanisms. The inspection methods and the extent of NDE applied shall be evaluated to ensure they can adequately identify the damage mechanisms and the severity of damage.
Standards recommend the development of piping system drawings, and isometric or oblique drawings provide a means of reference, identifying the location and orientation of piping lines. Also, general service conditions, process flow, size, material specification the location of key fittings such as valves and orifices etc, along with piping weldments including butt and nozzle joints and piping supports (hangers).
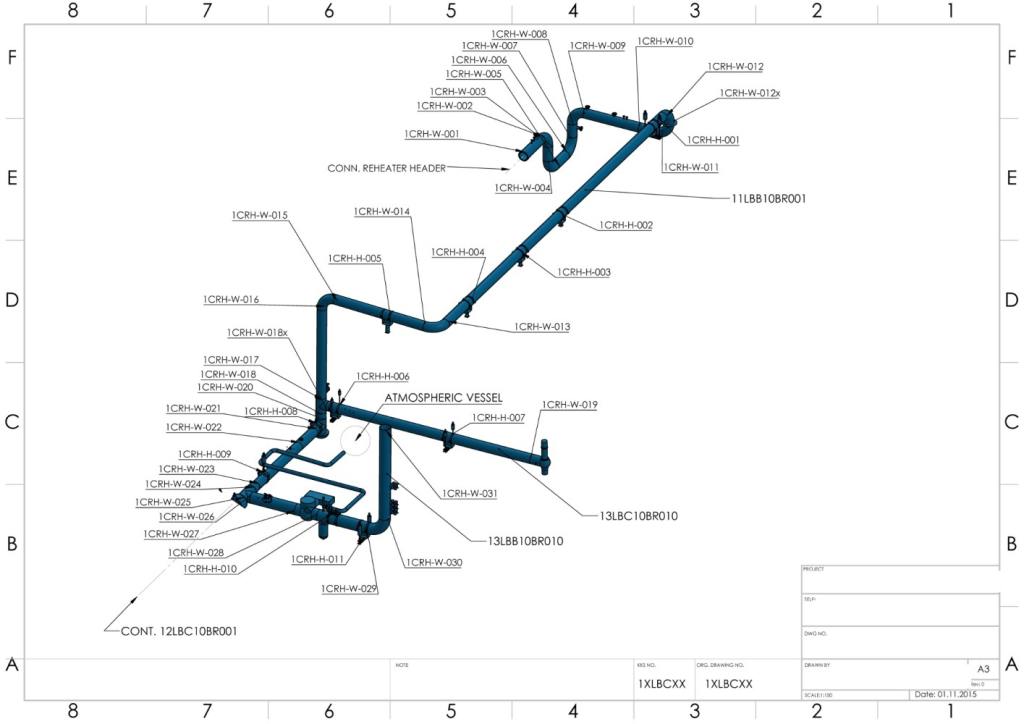
Standards govern, all inspection activities and applications, including pre-inspection preparation requirements, which shall be controlled in accordance with written procedures and applied by qualified operatives.
The standards deem that all inspection documentation relevant to system condition is maintained, and plant lifetime records are managed. A typical CPS program will generate large volumes of inspection reports and valuable related data, therefore establishing an electronic record system such as a ‘live’ database, when reviewing forward planning based on findings and CPS program management is recommended.
FIL – Web-Based Inspection Management Solution
Considering the detail and complexities faced in adopting and answering the guidelines of current standards and in support of our clients, AIS Field provides ‘FIL’, a digital-twin-based plant asset management system, built on a wealth of plant inspection and asset integrity management experience.
FIL is a web-based inspection management solution, developed for planning and maintaining records over the pre- and in-service life of a plant asset. The system simplifies the identification of plant items and enables the creation of intelligent graphics, linking critical plant items identified on system isometrics to a database management system.
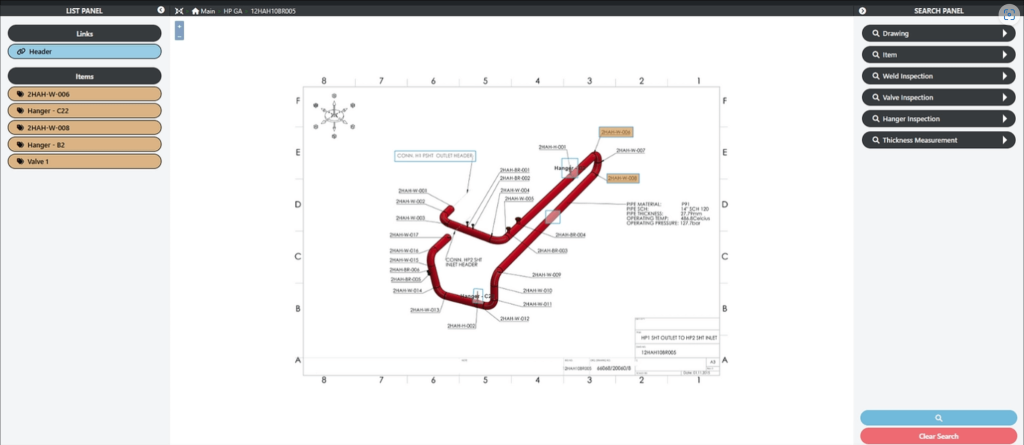
Tracking inspection and maintenance records is invariably a challenge to plant engineers. Maintaining system lifetime records and tracking plant item status when forward planning inspection and maintenance schedules, and unit shutdown/outage plans, especially when considering growing historical records, can be time-consuming and inefficient.
Using ‘FIL’, all plant item associated, QA documentation, maintenance and inspection files, and reports can be uploaded, stored, and accessed directly via system drawings and graphical links. In doing so, all activities and plant item STATUS can be tracked and monitored via this digital twin interface.