Inspection of Above-Ground Storage Tank (AST) – Advantages of In-Service Robotic Inspections
Inspection of Above-Ground Storage:
Storage tank bottom plates are inspected via Non-Destructive Testing (NDT) methods every 10-years as per API-653 regulations for thickness loss and corrosion. Inspection is generally made via visual inspection (VT), Ultrasonic Testing (UT) and Magnetic Flux Leakage (MFL). These methods detect the damages that occur to the structure during the operation. Thanks to NDT, the remaining wall thickness can be gauged without any further damage to the structural integrity, and repairs may be conducted if necessary.
Traditional Inspection Method for Storage Tanks
For fuel tanks, this inspection is mandatory. Traditionally, the inspection includes several steps:
- Planning: Since the tank is full of product and constantly in use, it cannot be taken out of service without prior planning. If the tank is incorporated into a production process, that production process may need to be altered or an alternative tank must be found.
- Tank emptying: Once necessary planning is made, tank is emptied. Depending on tank size, this can take substantial time. Moreover, it includes handling of hazardous product.
- Venting and cleaning: The tank that is emptied from liquid product will still contain remnants of flammable and toxic product, in addition to explosive gaseous environment and bottom sludge. Cleaning the tank and making it suitable for man-entry takes several weeks.
- Paint stripping: Prior to inspection, surface paint is stripped via water jetting or sand blasting.
- Inspections.
- Repairs (if needed): If inspection finds flaws, these are repaired.
- Repainting.
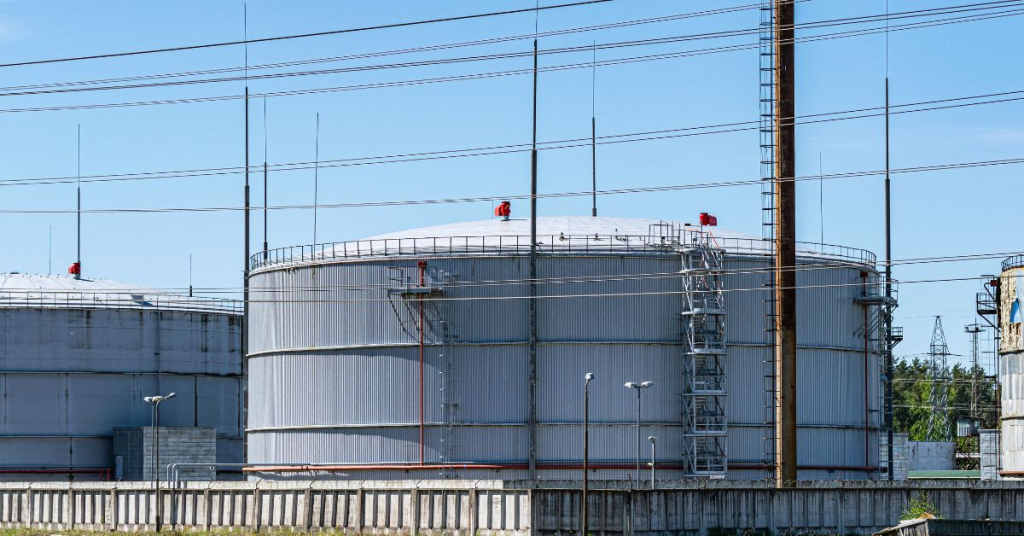
Drawbacks of Traditional Method
This lengthy conventional procedure, which had no alternative approaches until recently, has significant drawbacks:
- Tank is taken out-of-service. In refineries with constant production or busy terminals, taking a tank out-of-service means inefficiency, operation difficulties and lost profits.
- Manual procedure requires man-entry, which requires significant preparation effort (note that six out of seven steps in the conventional procedure are not directly related to the inspection).
- Preparation via planning: Operation planning should be made for an alternative tank that will hold the contents during tank down-time. Production and other operations are to be adapted to the reduced storage capacity during tank is out of service.
- Tank itself is to be prepared prior to inspection. Degassing, cleaning and sludge reduction principles are stipulated as per API 653. Special equipment such as ex-proof fans are to be used. Ventilation may required to be carried out for several weeks.
- Hazardous tank contents, including toxic fumes and sludges are released. These result in emissions, environmental pollution and additional handling costs.
- Confined space man-hours are required, causing OHS risks.
Robotic Inspection of Above-Ground Storage Tank
Thankfully, technological advancements have made elimination of all these problems possible. AIS Field introduces RUVI OilDiver, our zone-0 ATEX certified robot that can safely dive into explosive fuels and do in-service bottom thickness inspections via its UT sensors and cameras.
- Zero planning required. Facility continues its business as usual while our team carries out the tank inspection. All of the additional steps are eliminated.
- Zero downtime. Our customers can continue operation with their tank during the inspection (which already takes significantly shorter). In fact, we encourage them to.
- Hazardous tank contents, toxic fumes and sludges, are not released, since we leave the tank contents intact.
- No confined-space man-hours, RUVI OilDiver takes care of everything.
But, what if the tank bottom is found compliant and not requiring repairs?
This is where our approach really shines. RUVI Oildiver’s robotic tank bottom inspections are fully compliant with API 653. If repairs are found to be not required, bottom inspection data are added to the roof and shell evaluations for a full API 653 report, without ever stopping facility operation or emptying the tank.