Robotic Inspection in Non-Destructive Testing
Non-Destructive Testing (NDT) fulfills a crucial role in ensuring the safety and integrity of structures, machinery and materials in various industries. Emerging technologies and changing trends lead to significant advancements in the field of NDT as technology evolves. NDT covers a range of techniques used to evaluate the properties of materials, components and structures without causing any damage.
NDT is used during the entire life cycle of components, systems, products and facilities, starting from design, raw materials control, manufacturing and assembly processes, in-service inspections, condition monitoring management and remaining life assessment of components, systems, products and facilities.
NDT can be performed during or after production and manufacturing and even on equipment in service.
In manufacturing, NDT practices are used to ensure that parts are suitable for a desired function, ie. that they will last for a given time in operation. In-service NDT practices can be used to assess the current state of damage, monitor damage mechanisms and make informed decisions for remaining equipment life assessments [e.g. Risk Based Inspection (RBI), Fitness for Service (FFS).
Why Non-Destructive Testing (NDT)?
There are several reasons leads to Non-Destructive Testing:
- Assures Security: Periodic NDT inspections prevent failure and allow a proactive approach in equipment operation.
- Quality Assurance: In production, NDT ensures the product is up to required standards.
- Cost Savings: By preventing failure but also unnecessary repairs/replacement, NDT more often than not pays for itself.
- Compliance: Many authorities now require or advise NDT in inspections due to its much higher precision.
Some NDT techniques, such as visual inspection, eddy current testing (ECT) and ultrasonic testing (UT), thermal imaging can be automated, and this fact brought forth increased investment in robotic NDT systems for these methods.
Why Robotic NDT?
Replacing human operators who are prone to mistakes and OHS risks with much more reliable robots bring forth many advantages that improve precision, efficiency and safety. In addition, robots allow inspections to be carried out in places not easily accessible to operators and remove people from potentially hazardous environments. Thanks to all these, usage of automation and robotic inspection, especially to deal with difficult to access, remote and hazardous applications are gaining foothold.
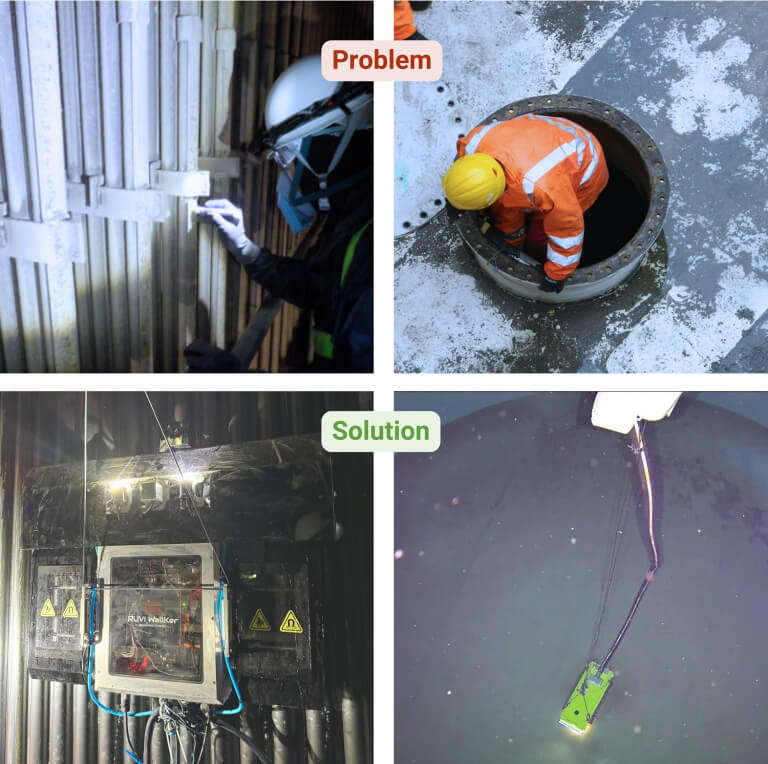
- Even More Precise: Unlike human operators, robots can easily collect thousands of data-points, and are fully reproducible. For example, our RUVI Wallker system can collect a data-point every 1 mm from waterwalls, which is impossible for a manual application.
- Remote Inspections (No OHS Risks): Working at heights, in confined spaces or dangerous environments are no issue for robots. For example, our ATEX-certified RUVI OilDiver simply dives into oil tanks toxic and explosive hydrocarbons for bottom inspection while our RUVI WallKer climbs waterwalls without needing scaffolds.
- Much Faster Inspections: Automated robots can cut inspection times almost ten-fold. Remember, in industry, time is money!
- Detailed Reports: Robotics NDT can provide comprehensive reports, providing information on every minute detail. All iterations of inspection reports can also be stored indefinitely and compared with each other thanks to our web-based Inspection Management System, fil.