Tank Inspection – Everything You Need to Know About Tank Floor Inspection
Tank inspection is a must in the industrial world to keep your valuable tanks safe and operational. These tanks which hold oil, chemicals or other hazardous materials are big investments, with construction cost often exceeding one million dollars. Uninterrupted operation is key to maximize return on investment and minimize environmental risks like leaks or spills. By inspecting tank structures especially the floors regularly, companies can detect early signs of corrosion or wear and prevent costly downtime and comply with industry standards like API 653. In this article we will cover everything you need to know about tank floor inspection including the latest in robotic inspection technology.
What is a Tank Inspection?
Inspection means careful examination and scrutiny. In an industrial context, inspection procedures are almost always guided by regulations. Industrial assets are not only expensive pieces of equipment, they also provide constant cash-flow; as long as they are in service. This is the main idea of inspection: to prevent future time lost. In that sense, inspection pays for itself. Being important industrial assets, storage tanks are inspected to ensure safe, uninterrupted and long operation.
Why is Tank Inspection Important?
Industrial tanks that store oil, oil derivatives or chemicals are expensive assets. A tank that is small to average in size costs at least several hundreds of dollar to build with most tanks that are currently operated on the field exceeding 1 million dollars in construction cost. To make the most this significant investment, tanks should stay operational at all times. Inspection is the only way to prevent unexpected leakages and ensure uninterrupted operation. Moreover, leakages in fuel and chemical tanks cause significant environmental hazards. This makes tank inspection crucial for green industry and zero emission.
How Often Should a Tank Be Inspected?
As per API-653 regulations guiding tank inspection, storage tanks require full inspection for thickness loss and corrosion every 10 years under normal conditions. Inspections can be carried out more often than that if the asset owner predicts a heightened risk.
How to Inspect a Tank?
Tank inspections are crucial for safety, reliability and longevity of industrial storage units but the method of inspection can make all the difference in efficiency. Traditional Non-Destructive Testing (NDT) methods like Visual Inspection (VT), Ultrasonic Testing (UT) and Magnetic Flux Leakage (MFL) have been the norm for years. But these methods require tanks to be completely emptied and taken out of service for several months which although effective introduces downtime and risks to environmental and safety factors.
Thanks to technology, robotic systems like the RUVI OilDiver offer an alternative. These systems can inspect the tank floor without emptying the tank so companies can stay in operation. In the next section we will look at traditional methods and the RUVI OilDiver, the benefits and the advancements in tank floor inspection.
Traditional Methods
Non-destructive Testing (NDT) is the industry standard since it makes possible to gather a significant amount of data without causing damage to the structure. Tank inspections are generally made via visual inspection (VT), Ultrasonic Testing (UT) and Magnetic Flux Leakage (MFL). These methods detect the damages that are present in the structure so that they can be fixed afterwards. Since it is impossible for these methods to inspect tank floor when the tank is full, traditional methods require the tank to be fully emptied and put out-of-service for several months, but this is considered as a decent trade-off since this procedure helps to prevent future unexpected failures. However, environmental and safety risks that arise from this process cannot be fully mitigated.
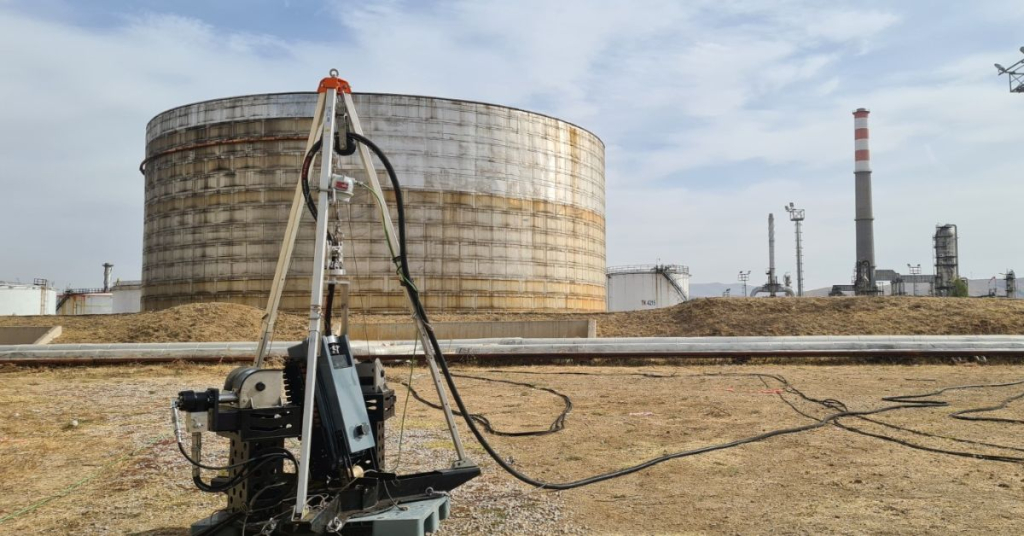
Ruvi OilDiver – A Robotic System Designed for Tank Floor Inspection
Recently, technological advancements made it possible to carry out tank floor NDT without emptying the tank. Our advanced system, RUVI OilDiver, is able to dive into a fuel tank that is full with explosive content, thanks to its Zone-0 ATEX certification. This makes possible UT and visual inspection of the tank floor, without taking the tank out-of-service for even one day.
Ultrasonic Thickness Measurement and Corrosion Mapping with RUVI OilDiver
RUVI Oildiver provides API-653 compliant reports. It can fully map the tank floor with both thickness and visual data, detecting exactly where and on which floor plate corrosion had occurred. Thanks to the highly accurate thickness data, asset owners can gauge if and where repairs are required. Data received from RUVI Oildiver inspections makes Risk Based Inspection (RBI) possible. Robotic Inspection can determine “good actor tanks” which do not and are unlikely to require repairs and maintenance. That way, inspection and maintenance budget can be diverted to “bad actor tanks” which need the most attention. This is also crucial for insurance purposes since the data can be used to reduce uncertainty and decrease the insurance premiums.
API 653 – What is API 653 Standards for Tank Inspections
API 653 is an industry standard set by the American Petroleum Institute (API) for the inspection, repair, alteration and reconstruction of aboveground storage tanks for petroleum and other liquids. While the design and construction of these tanks are covered by API 650, API 653 is for the ongoing integrity of the tanks. It specifies inspection frequency, types of inspections and what to do if any defects are found. API 653 compliant inspections are mandatory for safe tank operation and is often required by national regulations in Turkey. It also emphasizes documentation so API 653 is a must have framework to ensure tanks are safe, reliable and in continuous service.
API 653 says in-service tanks must be inspected every 5 years. More detailed inspections including Non-Destructive Testing (NDT) of the tank floor for thickness and corrosion must be done every 10 years under normal conditions. In the past this would mean taking the tank out of service for a long period of time but with advanced robotic systems like the RUVI OilDiver you can do it without any downtime.
What is API 653?
American Petroleum Institute (API) 653 is a standard that guide inspection, repair, alteration, and reconstruction of aboveground storage tanks of petroleum products and other liquids. Note that initial tank design and construction is guided by API 650. API 653 stipulates the frequency and types of inspections required to ensure the integrity of storage tanks. In addition, if issues are identified, maintenance and repair of tanks are also to be made in accordance with API 653. API 653 also provides guidelines for documentation; thus, an API 653 compliant inspection and reporting is necessary for tank operation. Turkish regulations also cite API 653 and require API 653 compliant inspections.
How often is API 653 inspection?
Every five years, in-service inspections are to be carried out. Under normal conditions, every ten years, bottom-plate thickness NDT is required for above-ground tanks. As mentioned, these traditionally require lenghty out-of-service NDT operations. Not anymore, thanks to the RUVI OilDiver.