Waterwall Inspections With A Robotic Crawler
Waterwall inspections are important especially when it comes to inspecting a boiler’s waterwall thickness.
The boiler is an equipment that is used to generate high temperature and/or pressure steam for various process uses. The boiler is the bread-and-butter of thermal power plants, with the turbine. Boiler walls are used to transfer combustion heat from the furnace to water. This high-energy water can then be used for various purposes, such as energy production at a turbine.
Also called waterwalls or evaporator walls, boiler walls are water pipes directly in contact with the furnace and they typically get exposed to high temperature, pressure and also fluctuations of both. Even though they are built to withstand these conditions, over time, boiler walls may lose thickness in the furnace side due to exposure to harsh conditions.
When a boiler wall gets too thin, it can fail, starting to leak high pressure water vapor. Not only is it dangerous, but it is also extremely costly when that happens, since the process needs to stop for the leak to be repaired. For energy plants, consistent production is the key; and since equipment failures eat into a plant’s profits, every plant has a planned maintenance schedule one or two times per year. A non-inspected boiler wall at any moment and from any point, but if inspected and weak points detected are subsequently repaired, risks can be minimized with waterwall inspections.
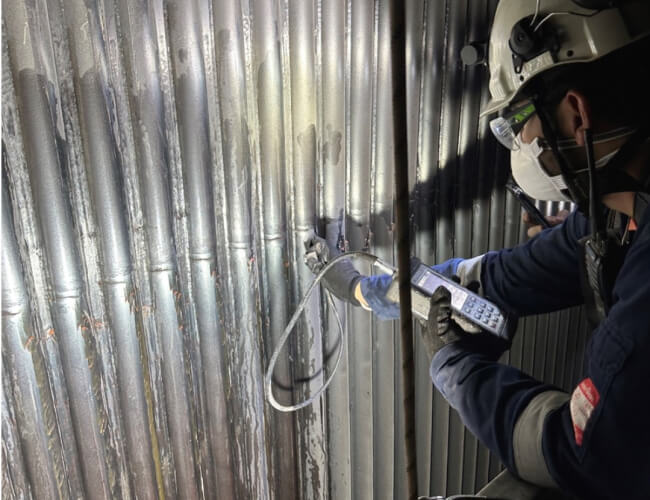
Waterwall Inspections – Ultrasonic Thickness Inspection
One of the most important routine inspections for boiler walls is ultrasonic thickness inspection. Via ultrasonic thickness inspection, failures may be predicted and proactively repaired. Traditionally, a couple dozen measurements are taken from the most critical points and then they are compared to the minimum thickness values from the guidelines. If thicknesses are found to be insufficient, repairs are conducted. However, the traditional approach has a number of shortcomings.
Most importantly, manual operation can only obtain limited data points. It is not humanely possible to cover the whole area. This means that even the best manual inspection will leave many blind spots.
- Manual inspection has reproducibility issues. Different firms and operators and even the same operator on a different day can report slightly different thickness values. Sometimes, even these slight differences prove to be costly in the long run.
- Manual inspection has OHS risks. The points to be inspected are more often than not located at heights or in confined spaces. This means dangerous operation and higher personnel cost.
- Manual operation is both slow and expensive. It also requires scaffolding, which has a very high cost and adds to the operation time.
The Solution: Magnetic Crawler Robots
Advances in robotic technology have made possible many innovative solutions to old problems. For waterwall thickness measurements, our magnetic crawler robot, RUVI Wallker, equipped with an Ultrasonic Thickness (UT) sensor and camera can do what a human operator does, without any of the drawbacks.
- Automated operation is 100% reproducible.
- Robots are immune to OHS risks. A magnetic crawler robot can safely operate at heights and in confined spaces, without endangering human life.
- Magnetic crawler robot is fast (10 m/min) and cover the whole waterwall system in just a couple of days. Since it attaches itself to the waterwall magnetically, it can ascend from the ground level, eliminating the need for scaffolding.
- Robotic inspection is not limited to a few data points. Wallker can collect data from every 1 mm while climbing, making possible a full mapping of the waterfall.
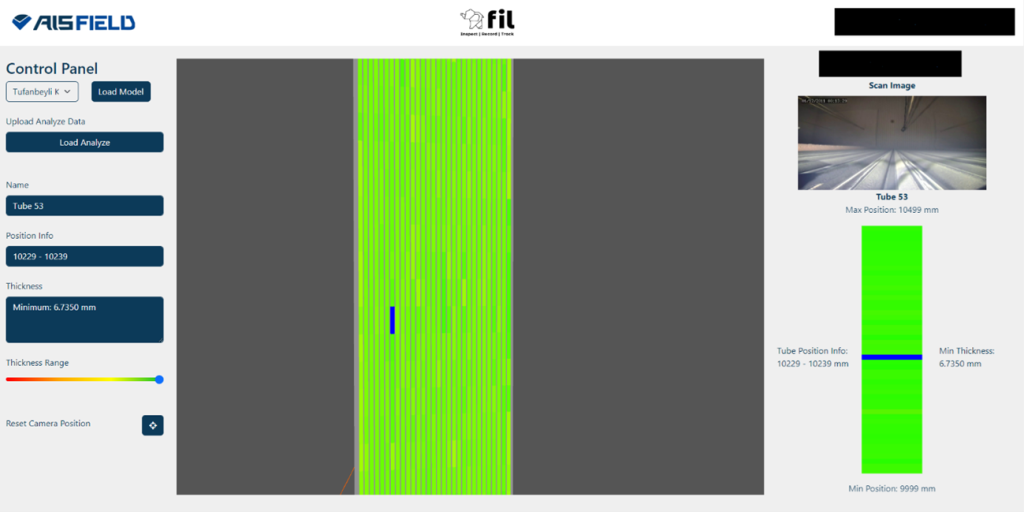
Robotic Magnetic Crawler Wallker’s operations can be divided into two areas:
- Operating Thickness Loss: More common practice is to get a full Wallker inspection yearly, during planned maintenance operations. That way, any problematic spots are detected and repaired. This also makes possible predictive maintenance, ie. predicting when a failure will happen or estimating the rate of thickness loss and planning maintenance to prevent future failure.
- Measurement of Nominal Thickness: During pre-service, or at any point of the service, the waterwall can be inspected by Wallker to provide a full thickness mapping. This data is provided to the customer indefinitely, providing a basis for all later inspections during the plant life.