Optimizing Maintenance Process for Storage Tanks
Industrial assets are the heart of any industrial facility. Since proper maintenance is the only way of ensuring safe and efficient operation for industrial assets, significant investment is made for developing more effective and optimized maintenance procedures.
Optimizing maintenance process for storage tanks is crucial due to various reasons. Firstly, most maintenance processed are tightly regulated. If we take storage tanks for example, API-653 inspections are closely tied to tank age and are mandatory. Moreover, there are tight regulations on exactly how the maintenance is to be conducted.
Secondly, routine maintenance is one of the best ways to extend an asset’s maximum lifetime and ensure its operational integrity. Tanks are expensive pieces of equipment which are used for holding valuable commodities. Thus, optimizing their maintenance process will pay off in the long run.
As competition grows in heavy industry, firms have found it lucrative to invest in cutting edge technologies which give them advantage over their rivals. Asset integrity is one of the most crucial fields for continuous, safe and profitable operation of an industrial facility. However, it cannot be said that it is getting the attention it deserves. Many facilities are reluctant to modernizing their routine inspection protocols.
Why Facilities are Reluctant to Modernizing Their Routine Inspection Protocols?
The main cause of concern is the vast amount of protocols already present in a plant. Heavy industrial facilities are more often than not quite large and complex, thus tinkering with already operational procedures can feel like a bad idea at first. Another concern is that heavy industry is a risky operation, thus operators have a tendency to err on the safer side and stick to older technologies. Lastly, new technologies are not always fully compliant with the regulations, which means that they cannot be implemented such regulation-heavy industries.
However, when it comes to adopting new technologies, a very well known fact is that early adopters get the lion’s share of the benefits and position themselves far ahead of their competitors. The longer companies hesitate, the more they risk being left behind in a rapidly evolving market.
Early adoption accelerates efficiency, boosts safety, and unlocks unprecedented levels of predictive insight. Those who take action first will thrive, while the ones who drag their feet will find themselves desperately playing catch-up, with increased price but decreased return. The market rewards bold moves, not hesitation. In this post, we go through why one should invest in the optimization of maintenance in storage tanks and how we can help you in alleviating your concerns.
The Importance of Modernizing Maintenance in Storage Tanks
When the time of maintenance comes, stressful days commence. Time is tight, costs are high and facility is losing money daily. In the case of storage tanks, there is possibly a very high opportunity cost of maintenance, since production in refineries is tied to available storage space.
Conventional inspection and maintenance all requires taking the tank out of service. This is because bottom is not reachable while the tank is filled with toxic and explosive liquid. But fortunately, new technology brought in robotic NDT practices, which made it possible to reach the bottom while in-service. Our RUVI Oildiver robot, thanks to its ATEX Zone 0 certification, is able to do fully API-653 compliant tank bottom inspection.
Moreover, our RUVI Wallker robot is able to climb tanks’ outer walls for full thickness mapping. Thus, modernizing storage tank maintenance practices means the customer is able to develop more efficient, safe and low-cost maintenance procedures without any downtime.
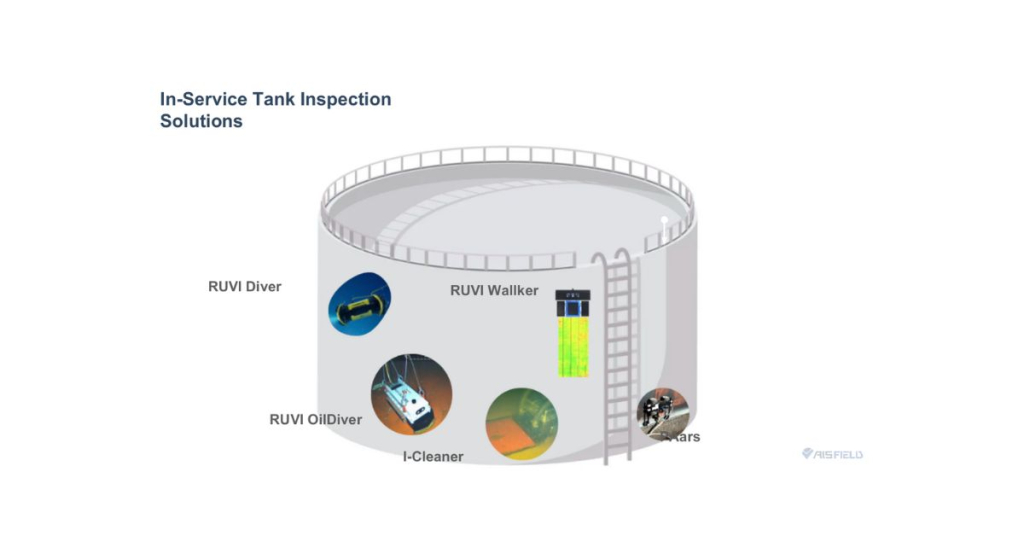
Common Maintenance Challenges
Challenges in tank maintenance are well-known for those who are in the sector. One cannot just simply get into tank, the tank should be emptied at first. This alone is a huge problem since if there is no back-up tank, the production will suffer. However, even when this is not a problem, planning for it is also brings in a significant problem.
Afterwards, preparing a tank for this process is long and cumbersome. Degassing, cleaning and sludge reduction are mandatory practices as per regulation. The tank is also to be ventilated via ex-proof fans for several weeks. One thing to underline again is the presence of toxic and explosive solids, liquids and gases/vapors during this whole process. These cause significant environmental risks, OHS concerns and handling costs.
In short, not only is conventional inspection and maintenance impractical, it is also dangerous, dirty and takes a long time. Optimization of conventional maintenance processes is not an easy task, since there are many aspects of it that can go wrong, adding it unpredictability.
Utilizing Technology to Overcome Challenges
In today’s world, robotics and AI are the names of the new revolution and cutting edge innovation is achieved in many sectors via integrating new developments there to that specific sector. Our team, well aware of all the short-comings of current conventional methods thanks to their vast field experience, have done just that. We utilize robotics and AI to decrease human errors, get procedures done faster, build more stream-lined inspection and maintenance operations and most importantly operate in places not possible for human operators thus minimizing the danger to human life.
Robots work with precision simply impossible for human operators, can collect hundreds of thousands time more data than human can, can safely climb to heights, can work in confined spaces, can dive into toxic and explosive fluids. Utilizing AI makes possible to analyze big data for predicting error mechanisms, making possible much more efficient maintenance practices. In the long run, putting together the vast amount of data collected by robots with the analyzing capabilities of the AI models, it will be made possible to build new and unprecedented inspection and maintenance protocols for storage tanks as well as other industrial assets.
Strategies for Optimizing Maintenance Process for Storage Tanks
Making the transformation to robotic extremely straightforward, the robotic inspection of storage tanks is much easier to manage than a conventional inspection. First of all, robotic inspection does not require thorough planning. Since the tank is not to be emptied, no back-up tank is needed. Tank content is left intact, so there is no need for ventilation or sludge management. There are also next to no emissions.
Robotic inspection can be decided only a couple days prior and is quickly finalized. If tank is found in good condition, fully API-653 compliant reports will be received without ever opening the tank. In case a tank requiring maintenance is detected, prior robotic inspection will have given thorough information on so that maintenance can be planned accurately and can be conducted quicker and more efficiently. Thanks to all these reasons, a robotic transformation for tank inspection and maintenance is extremely easy for and works wonders for optimizing maintenance processes for storage tanks.
How AIS Field can Help You?
As mentioned above, there are admittedly difficulties of attempting a robotic transformation for optimizing maintenance processes for storage tanks. To minimize the uncertainty, the company that is offering a robotic solution should be aware of the complexities present in heavy industrial processes.
The AIS Field team, with its vast field experience, is not only a robotic service provider but also is able to act as a consultant regarding the big picture of a plant. Working with such a seasoned team minimizes the risks of a robotic transformation while maximizing its benefits.
Our solutions are not cookie-cutter ones, but are tailor made on the field for real industrial conditions. Our robots are made to solve problems, and are designed to be fully compliant with regulations such as API-653. All our solutions are designed, manufactured and operated by us, thus they are fully optimizable to each customer. With its R&D capabilities, AIS Field is constantly developing new innovative solutions for pressing industrial problems.