Machine Learning in Non-Destructive Testing
Non-Destructive Testing (NDT) techniques are widely used for ensuring the safety and integrity of industrial assets. NDT makes it possible to analyze components without interfering with their structure. NDT is used pre-service as well as in service (e.g. Risk Based Inspection (RBI), Fitness for Service (FFS)) equipment to gauge damage state, mechanisms and estimate remaining equipment life. Especially in sectors such as petrochemistry, power generation and tank storage, which have very expensive equipment, 24/7 operation, valuable input/output and hazardous conditions, Non-Destructive Testing is one of the most important aspects to decrease operation risk and increase efficiency.
NDT, being very widely used and depended on technology, is always quick to incorporate new technological advancements to improve its robustness. Two most exciting fields that have seen significant technological advancements recently are robotics and artificial intelligence (AI). As well as incorporating robotics into NDT with solutions such as RUVI Oildiver and RUVI Wallker, AIS Field also works to incorporate AI for better NDT analysis and reporting performance.
Traditional Methods vs. Robotic Methods
Traditional approaches have several shortcomings which are time-consuming analysis, high potential for human error, limited adaptability to dynamic environments and high dependency on skilled operators. Machine learning can enhance traditional NDT techniques by automating defect detection and minimizing human error, also cutting costs.
The advantages of Machine Learning in NDT are:
- Automation and Efficiency: Machine learning models, especially neural networks, can quickly process large volumes of Non-Destructive Testing data and provide rapid, accurate defect detection.
- Improved Accuracy: In most cases, machine learning makes possible better analysis than humans. In our article titled “Development and Comparison of RNN, LSTM and GRU Neural Network Models for Automated Eddy Current Inspection of Heat Exchanger Tubes Using Real World Industrial Data”, recently published and presented in BINDT 2024, the machine learning models developed (RNN, LSTM, GRU) achieved accuracy levels over 98%, outperforming traditional rule-based software and human inspection (with GRU achieving the highest accuracy of 99.26%).
- Cost Savings: Automating the inspection process reduces the need for manual analysis, thus lowering operational costs by saving time and reducing the need for highly specialized personnel.
- Reduced Human Error: By removing the need for subjective human analysis, machine learning can reduce inconsistencies in reporting and ensure a more standardized evaluation process.
Machine learning in NDT at its current state also faces some challenges and has some limitations which will be mitigated over time with advancing technology:
- Data Quality and Availability: Machine learning models require extensive and well-labeled datasets to perform effectively. Gathering and labeling real-world data (such as the 10 years of data used in the AIS Field study) can be resource-intensive.
- Computational Demands: Training complex models such as deep learning architectures (RNN, LSTM, GRU) can require significant computational resources, both in terms of time and hardware (e.g., GPUs).
- Bias and Overfitting Risks: Without careful curation of training data, machine learning models may develop biases, leading to overfitting on specific types of defects or equipment.
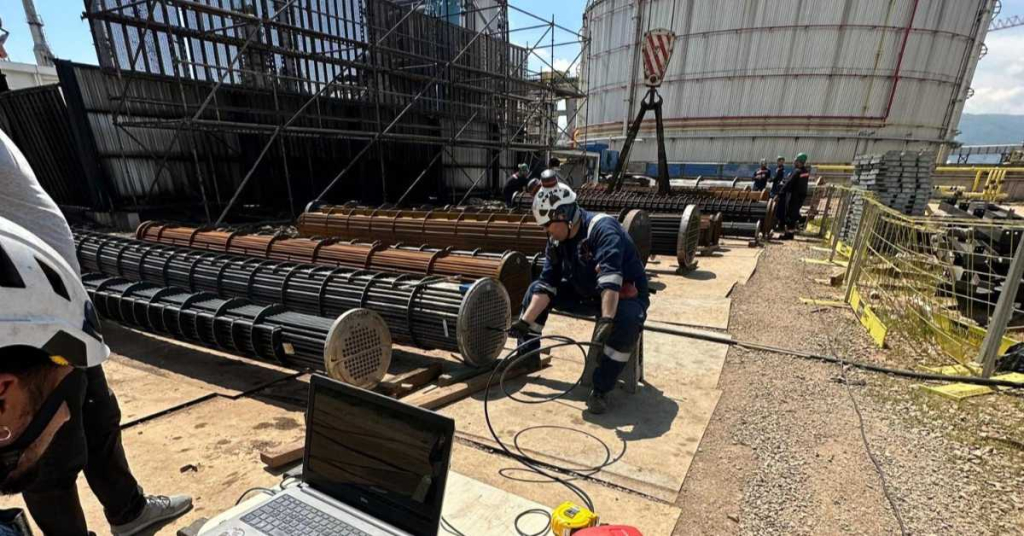
Recent Developments and Case Studies
AIS Field R&D Department contributes to the scientific literature on the use of machine learning in NDT. In our recent study, machine learning models were used for the data analysis and reporting of eddy current testing (ECT) in heat exchanger tubes.
Real-world inspection data from 89 heat exchangers have been gathered. From the data, more than 100.000 potential defect areas have been extracted using advanced signal processing methods. For the machine learning study, three bidirectional neural network architectures have been used: Recurrent Neural Networks (RNNs), Long Short-Term Memory networks (LSTMs), and Gated Recurrent Units (GRUs). It has been determined that GRU is the most accurate model among the three with 0.9842 general accuracy, followed by LSTM (0.9770) and the least accurate was RNN (0.9689). The ranking stayed the same for both ferrous and non-ferrous models.
False positives exceeded false negatives, underlining the prioritization of safety by the machine learning models. It has been shown in the study that with GRU models it is possible to reach 98.55% defect detection for ferrous and 99.89% for non-ferrous tubes. These results show that machine learning models significantly outperform human experts as well as traditional rule-based software systems in both accuracy and speed.
The Future of Machine Learning in Non-Destructive Testing
Increased Integration with Robotics: Machine learning models will likely be integrated into robotic systems for autonomous inspection. One example of such a development is AIS Field’s efforts to make use of machine learning to localize robots and reduce the time needed for NDT data analysis in storage tanks. This integration can reduce the need for human involvement in hazardous environments.
Predictive Maintenance: Machine learning could enable the transition from reactive to predictive maintenance, predicting when and where defects are likely to occur based on historical data and real-time analysis.
Enhanced Defect Characterization: Moving beyond detection, future advancements in machine learning could allow models to characterize the type, size, and severity of defects with greater precision, enabling more targeted maintenance strategies.
Machine learning offers significant advantages for NDT, from improved accuracy and cost savings to increased safety through automation. While there are challenges, particularly regarding data quality and computational demands, the potential for further advancements makes machine learning an essential tool for the future of NDT.
As industries continue to digitalize and automate, the role of machine learning in NDT is likely to grow, transforming how inspections are conducted and contributing to safer and more reliable industrial operations. Moving maintenance from reactive to predictive will do wonders for better workplace security and lessened environmental impact. In that sense, the future of NDT indubitably lies in the incorporation of robotics and AI.